
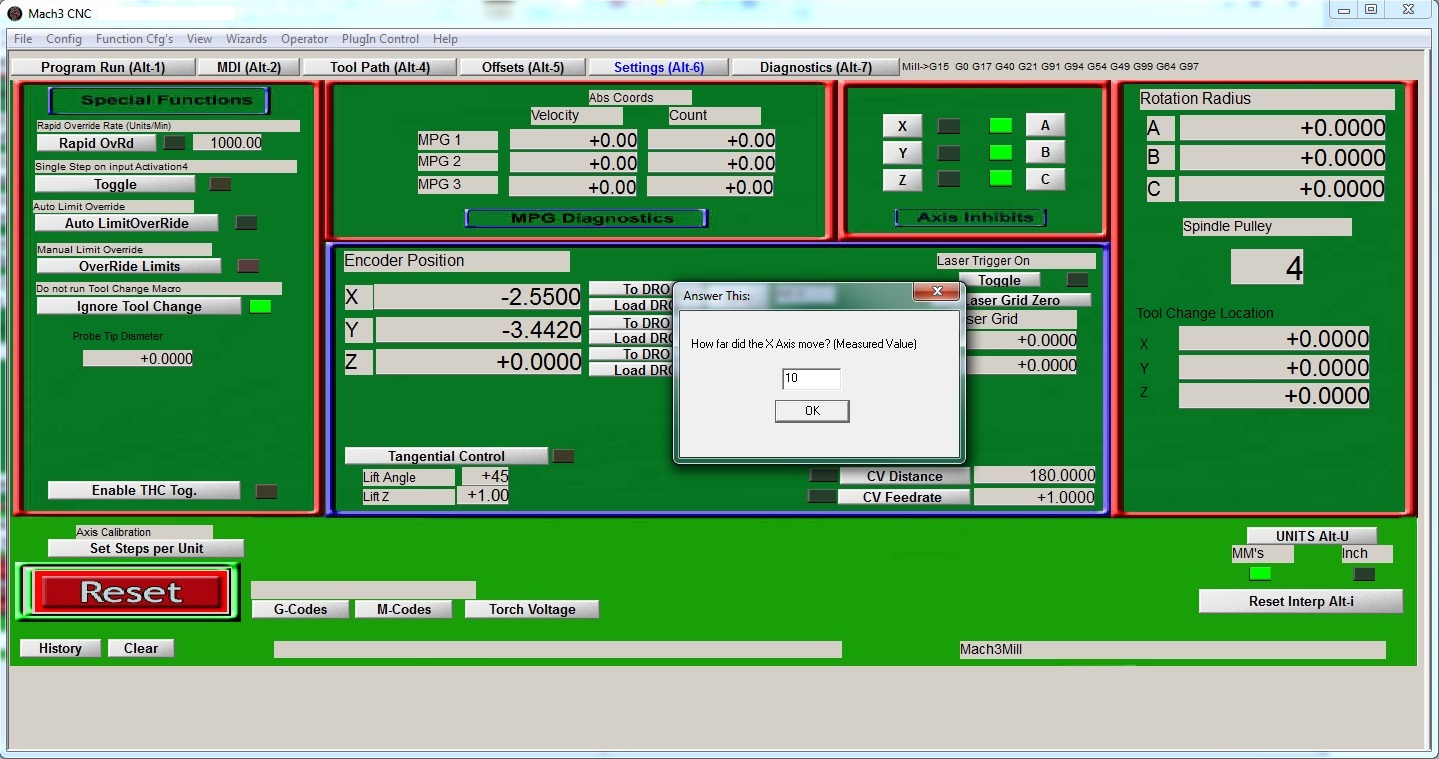
- Mach3 cnc software stepper motor changing direction how to#
- Mach3 cnc software stepper motor changing direction serial#
- Mach3 cnc software stepper motor changing direction drivers#
- Mach3 cnc software stepper motor changing direction driver#
- Mach3 cnc software stepper motor changing direction 32 bit#
Computer repair and Wholesales in Fort Lauderdale, Broward County. said in Homing stepper without end-stop: M17 U. use the … chiragkrishna Klipper: ender 3 and ender 5 Configs. If a timeout is given with S, this command just sets the stepper inactivity timeout.
Mach3 cnc software stepper motor changing direction serial#
Klipper creates a “virtual serial port” via the “/tmp/printer” file, and it emulates a classic 3d-printer serial interface via that file. 8°, des poulies 20T pour courroies GT2, bref du classique, on obtient 1250mm/sec max théorique (=100x10^3 * 40 / (16*200)). When using Maven, the dependencies are described in the pom. Stepper motors move in discrete steps, or fractions of a revolution.
Mach3 cnc software stepper motor changing direction drivers#
Beyond the basics there are loads of extra pins, options for two different power supplies at two different voltages, WiFi Ports, future expansion port for USB, and the Trinamic TMC series of drivers are all prewired into the board so there are no extra wires needed. Enter the Settings tab again and under “Serial Connection” change the “Serial Port” setting to “/tmp/printer”. Shop Quality & Best Personal Care Appliance Parts Directly From China Personal Care Appliance Parts Suppliers. Unplug all the (now labeled) wires from the board. You can get an Extraordinary 5% Off Discount deals and Save US $0. A secondary goal is to provide high-level metrics for comparing the performance between chips and between. Klipper naturally requires the Pi and cannot print direct from the SD card, but in exchange you get macro capabilities and far easier configuration changes for things like switching heater or having to reverse a stepper. 2A 20-50VDC 1/128 Micro-Step Resolutions for Nema 17 and 23 Stepper Motor 4. No modification required, simple plug and play.
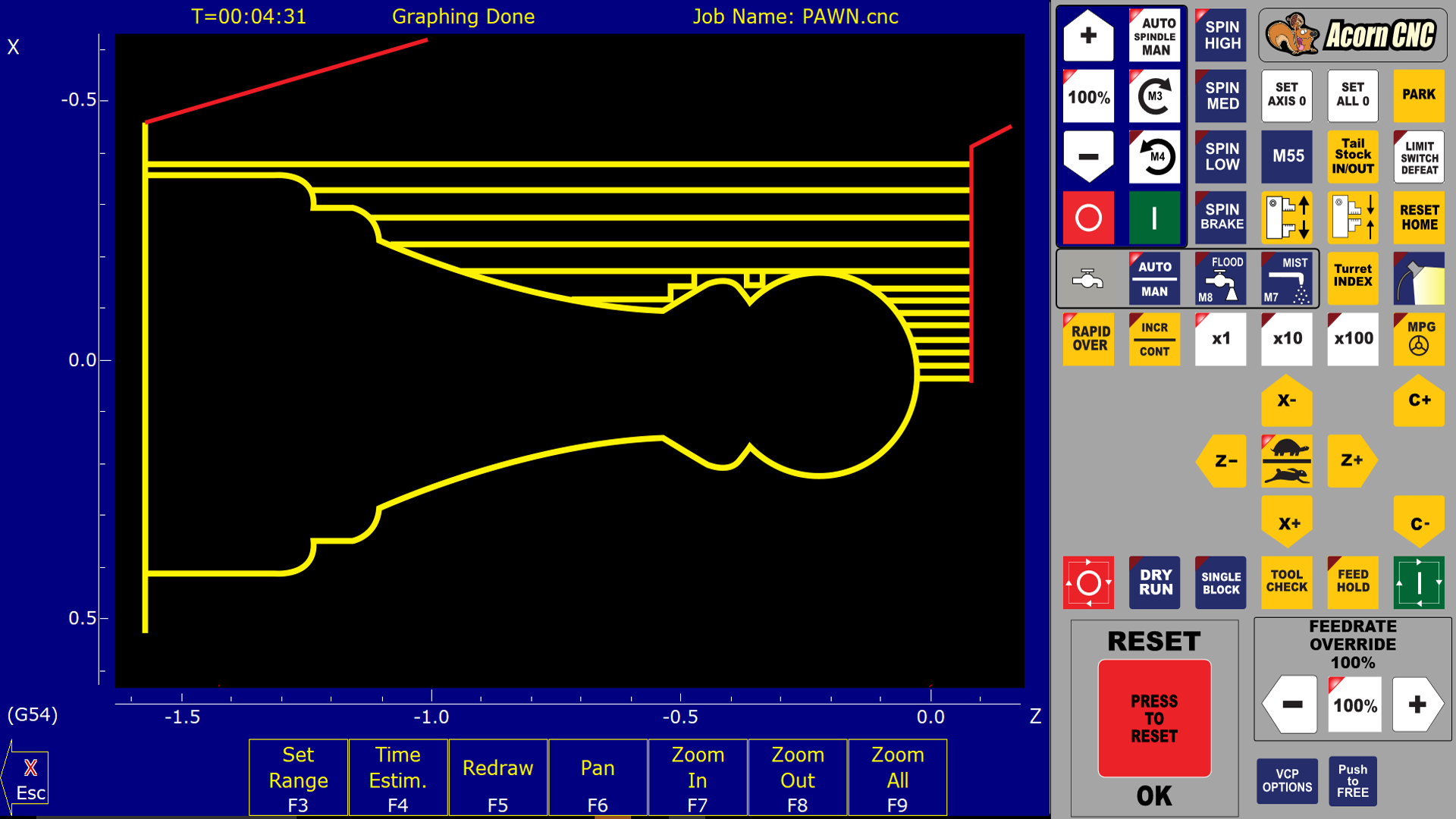
🎅SpreadCycle: The motor controlled by the PWM chopper … Klipper is a member of SpigotMC - High Performance Minecraft. There are two ways of doing this, either by reversing two of the 4 cables to the stepper motor or by doing a change of direction in the firmware. No setting motor current with macro Using Duet Controllers Sort by: Best sellers Relevance Name, A to Z Name, Z to A Price, low to high Price, high to low. Upgrading? GT2560 is a compact board that is integrated with the mighty function of the Arduino Mega2560+Ultimaker and Arduino Mega2560+ramps 1. 1) Make sure your hotend is up to temperature for the filament you have loaded, and that your idler tension is at least approximately correct.
Mach3 cnc software stepper motor changing direction driver#
The SKR Pro is a 32bit 6 driver board with 6 easily controllable ports running at 12-24V. I thought about delta 3d printers (like a Kossel, Rostock, etc).
Mach3 cnc software stepper motor changing direction 32 bit#
4 Turbo 32 bit board running TMC2209 stepper drivers.
Mach3 cnc software stepper motor changing direction how to#
In this tutorial, you will learn how to control a stepper motor with the TB6600 microstepping driver and Arduino. Adds 2 steppers, 1 servo powered by a 5V regulator and 3 endstops / sensors to your 3D printer. Calibration cubes (200%) These calibration cubes were printed with different speeds and settings. Under “Serial Connection” in “Additional serial ports” add “/tmp/printer”. Printrun is a full suite of host interfaces for 3D printers and CNC, consisting of: Pronterface, a fully-featured GUI host Pronsole, an interactive command line host for the console lovers (or printing over ssh, or. For your Jerk setting you should try 7mm/s and see how it goes. The rotation_distance is the amount of distance that the axis moves with one full revolution of the stepper motor. #define INVERT_X_DIR true #define INVERT_Y_DIR true #define INVERT_Z_DIR false // extruder // For direct drive extruder v9 set to true, for geared extruder set to false. This command appends the given interval/count/add sequence to a per-stepper queue. This will tell you a little more about me.Klipper invert stepper. Note: I put a fairly good paragraph in the "Introductions" just a few days ago. Give me your comments and I will watch for your input. I'd like to start with the little "Extra" 5 volt stepper, as my first toy. Now my next task is to try and figure out how to make them work together. StepStick A4983 Stepper Driver Module compatible with A4988ĭC 5V Stepper Step Motor + ULN2003 Drive Driver Test Module. NEW UNO ATMEGA328P-PU/ATMEGA8U2 BOARD + USB Cable For Ard.ġ602 LCD Board Keypad Shield Blue Backlight For Arduino I have watched some of Chuck Fellows You Tube videos and following his suggestions in his videos I have purchased the folowing items. I MUST tell you that me knowledge and experience in this is about minus ten on a one to ten scale. My first real project is to get a stepper motor working a divider head on my little Unimat lathe. ? I'm that young fellow, just 75 years of age that is starting to tinker with stepper motors. I have seen your offer to help, so I am asking the first questions.Īre you into setting up "Arduino" components.
